Welcome to the future of composite tubing.
Using a patent-pending closed molding process, we mold the part you need. This frees you to design in curves, create custom profiles, and take advantage of our unique design and strength characteristics.
Whether you need a curved tube terminating with a special profile, a fluid-bearing, bulletproof Kevlar™ part or a 24-foot public space LED embedded tubular work of art, our process allows you affordable design options never available before.
Contact us today, and let us help you achieve your design vision.
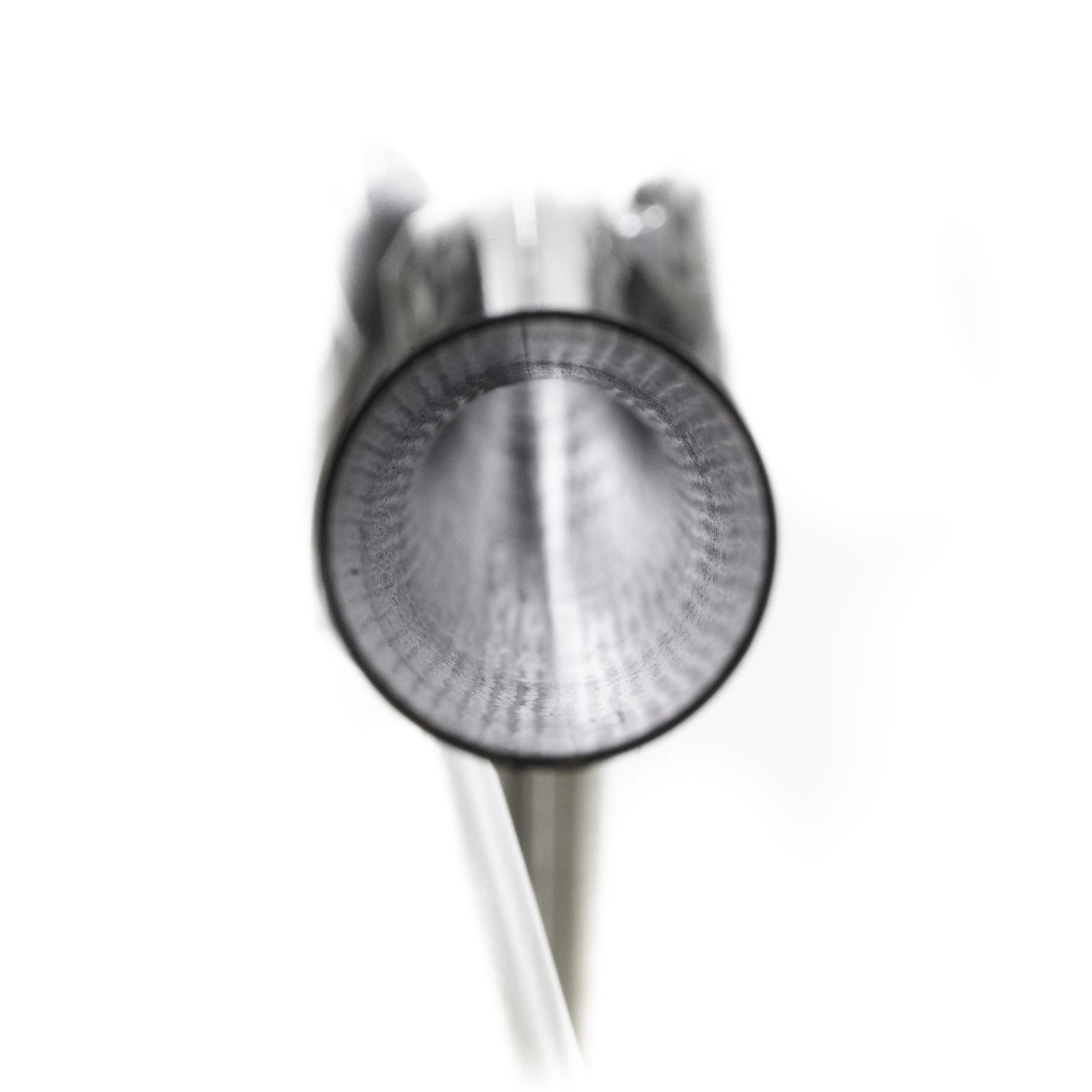
Braid choices and configuration properties
We work closely with A&P Technology, a worldwide leader in braided composite reinforcements. The fibers of A&P Sharx™ brand braided sleeves are continuous and mechanically locked, evenly distributing load throughout tubular structures. This means that TUBETEC tubes are stronger, tougher and more flexible than tubes made using other processes and fabrics.
The TUBETEC process also allows for specific braid angles. This means you can choose the orientation of the braid to achieve specific strength and structural properties. We can also vary braid angles or specific braid for each ply of a tubular structure. TUBETEC is all about achieving your design requirements.
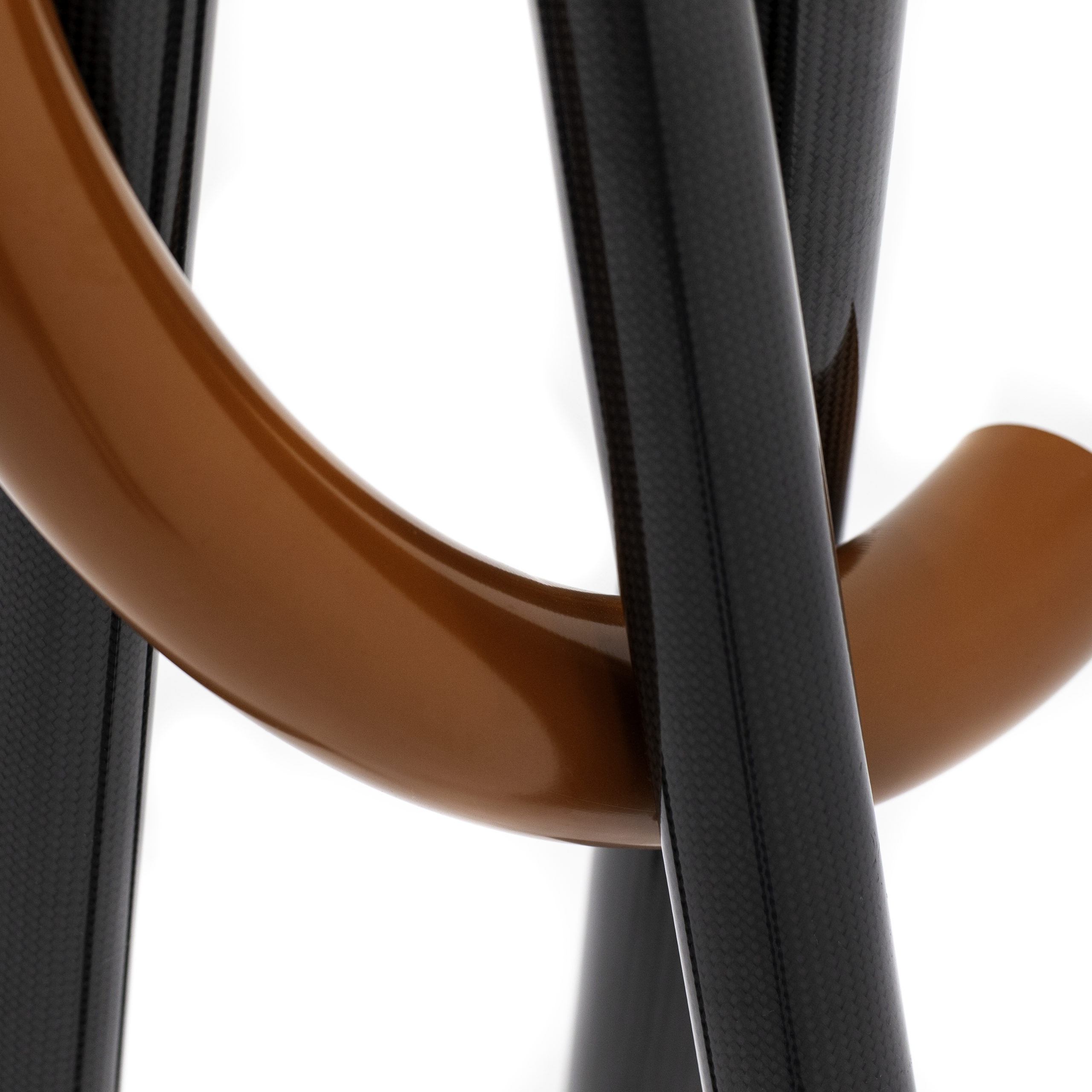
Resin choices
We proudly use Pro-Set and other products from the Gougeon Brothers family of epoxy products.
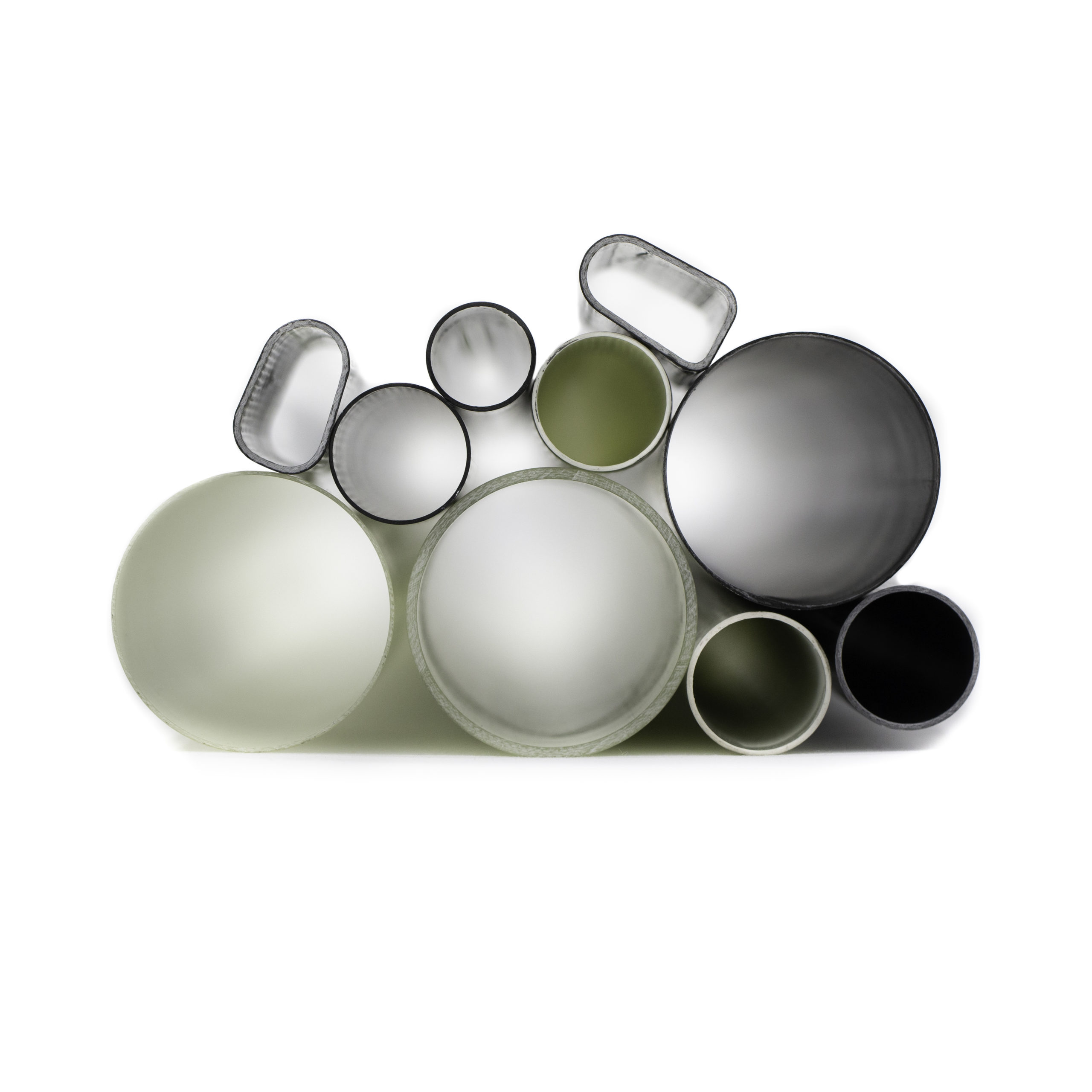
Diameter and length ranges
Currently, TUBETEC can make round tubes with diameters as small as 1”, as large as 4”, and incredible lengths to 20′ + .
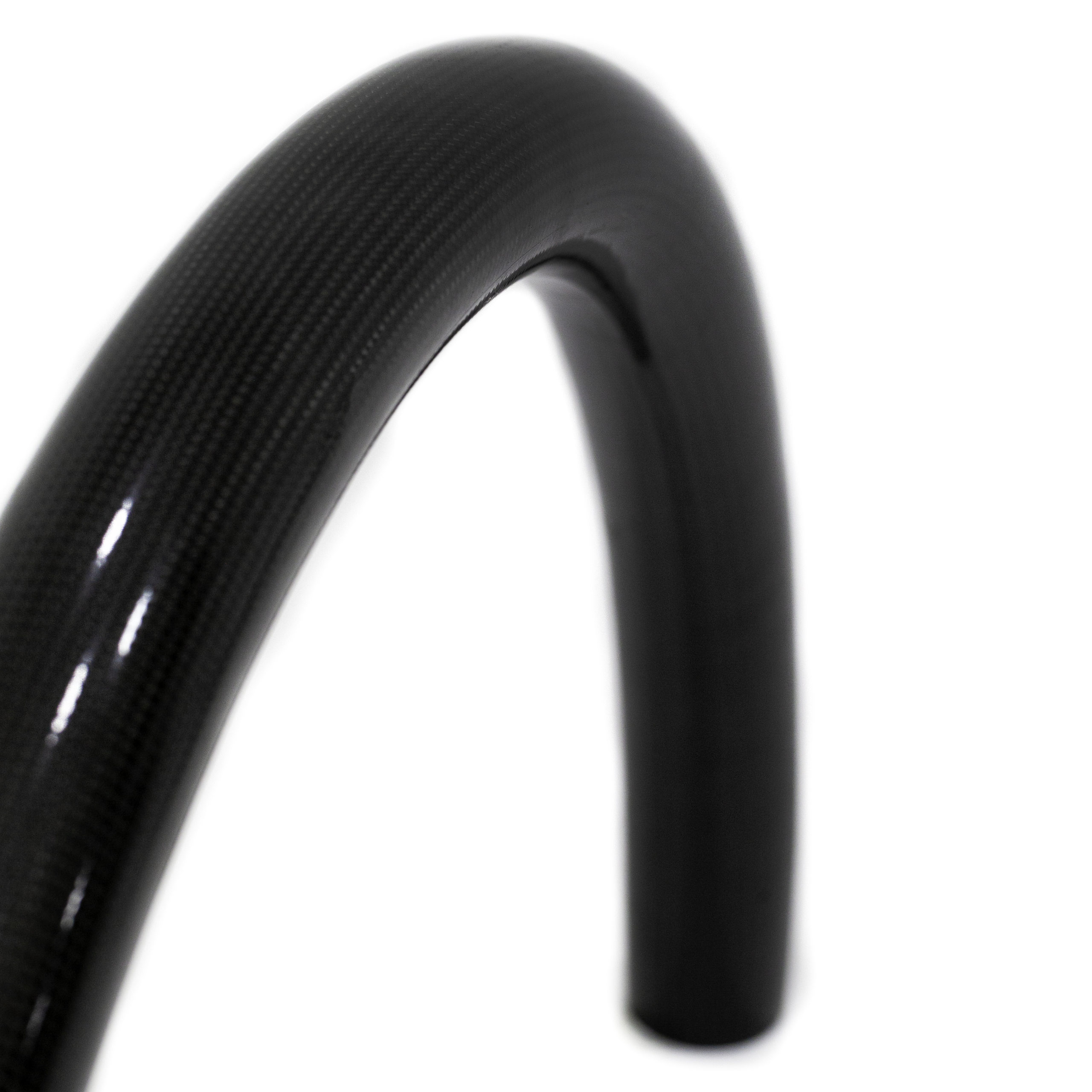
Curved tubing capabilities
One of the strengths of braids is the ability to conform to a curve. A&P SHARX™ braided sleeves, combined with the TUBETEC process, can be molded into gorgeous, amazing curves. TUBETEC curves can be constant, varying or transitional. There are limits to the radius of a curve, as the braid has to expand over the curve’s outer radius and contract within the inner radius. At TUBETEC, we love to see what’s possible, so bring us your curved tubular design and we’ll do our best to achieve it, quickly and affordably.
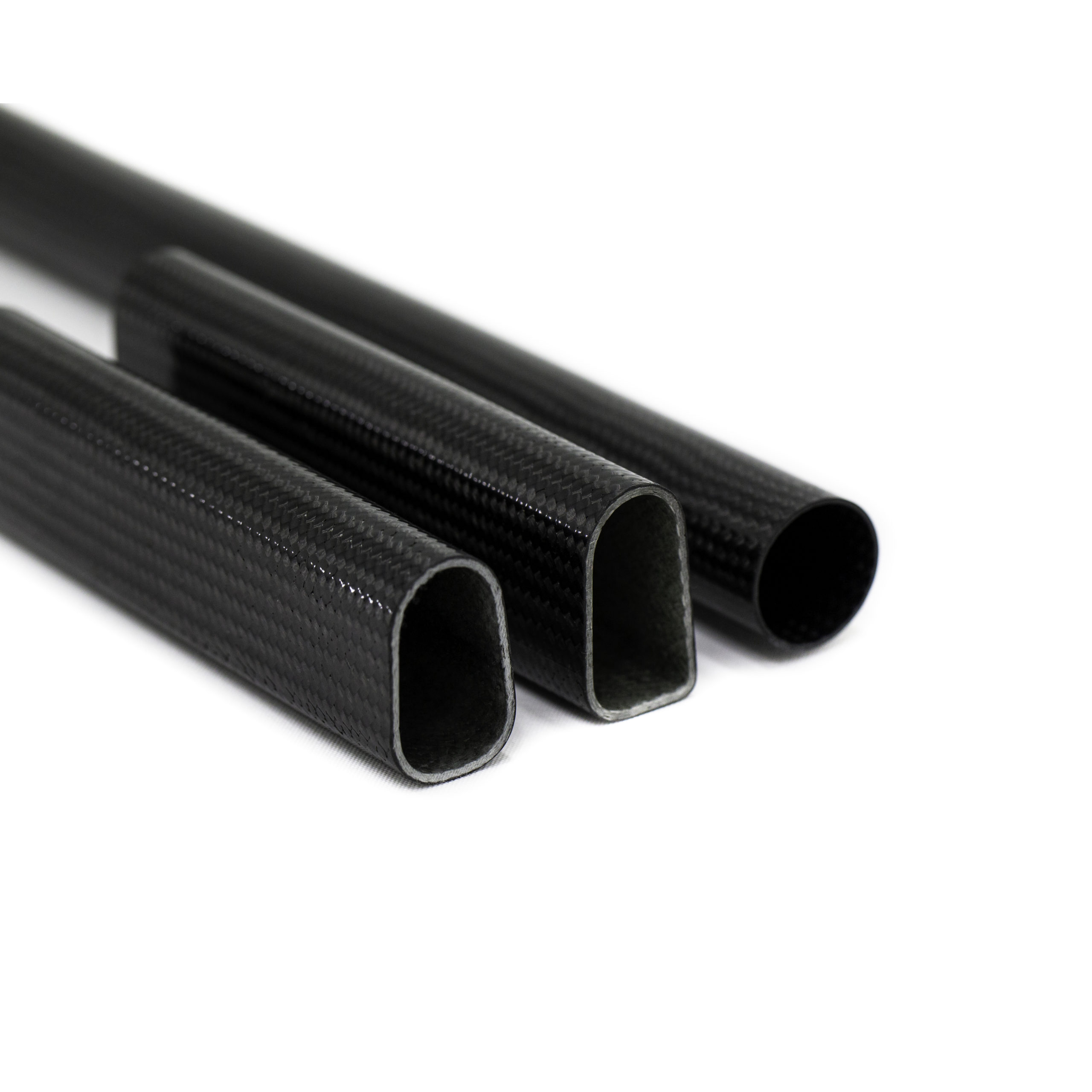
Profile capabilities
Beyond curves, TUBETEC can also mold custom profiles. It is easy to envision round, square or rectangular tubes. But how about oval, or quarter round, or square with an internal round channel, or…(you get the idea). There are some limitations to what you can do, but not many. At TUBETEC, we love to see what profiles are possible. Pushing the limits is what we do.
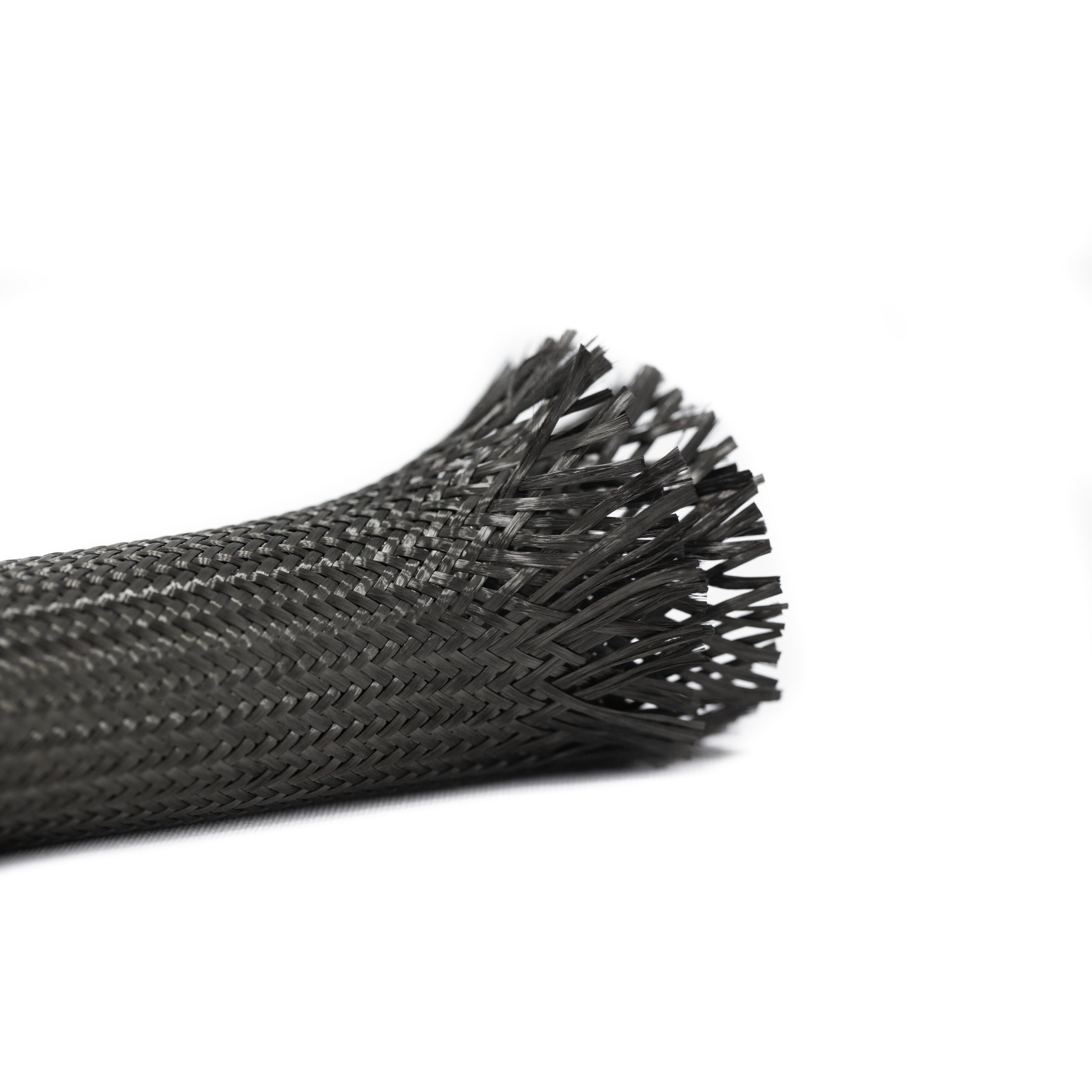
Material choices
We work closely with composite braid sleeves from A&P Technology. Stock material choices include carbon fiber, fiberglass and aramids (e.g., Kevlar™). A&P Technology also offers hybrid braids of carbon fiber/fiberglass and carbon fiber/aramids. Which means you can braid highly custom sleeves to achieve very specific braid properties and strength characteristics. Using the TUBETEC process, if it can be braided, it can be molded.
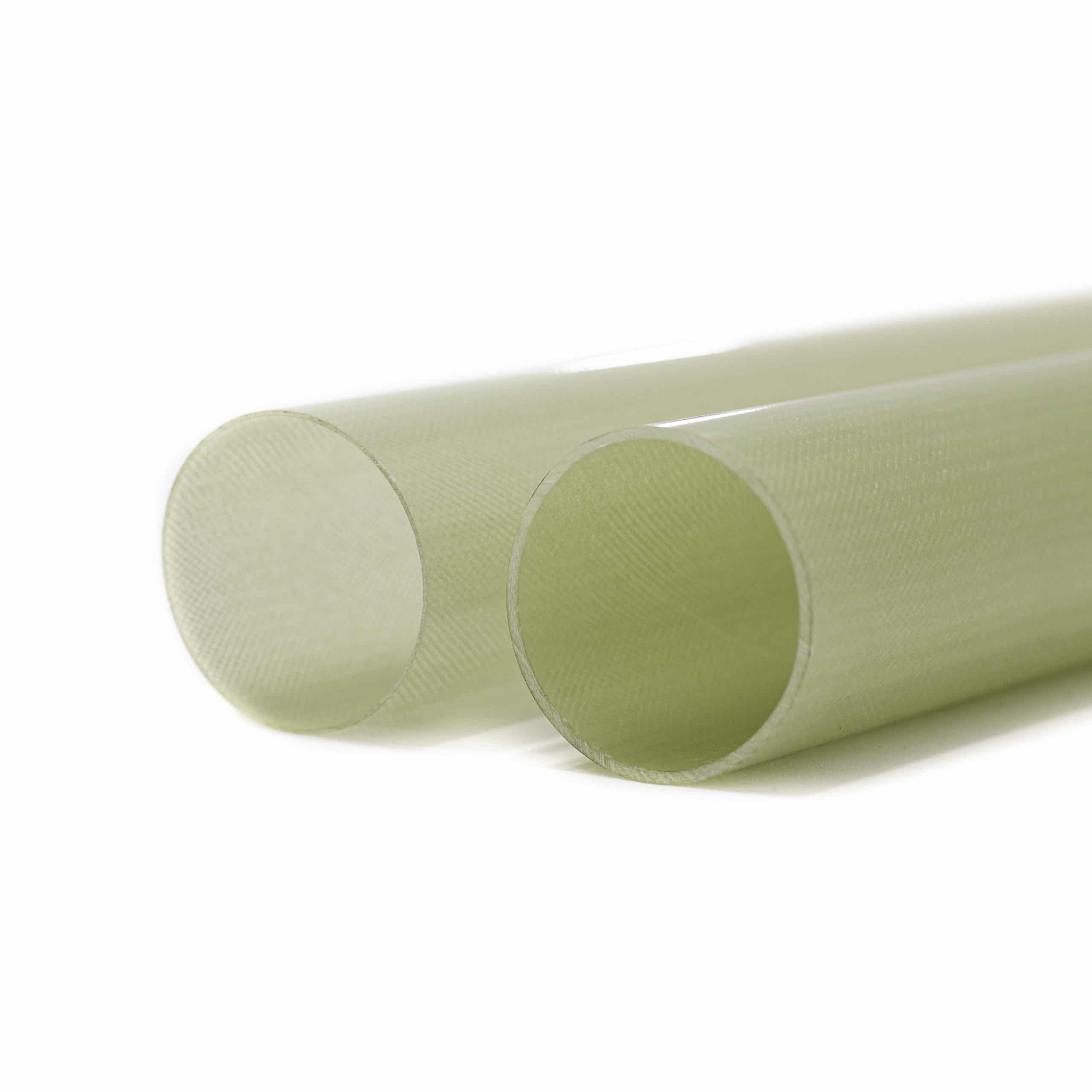
Ply and layup schedules
Another important consideration in producing an effective tubular part is how much strength you need and where you need it. By varying the number of plies and the placement of those plies, TUBETEC can make you a tubular part that is stiff in one area and flexible in another. We can even mix and match braids and placements to make incredibly unique parts that behave structurally and do exactly what you want.
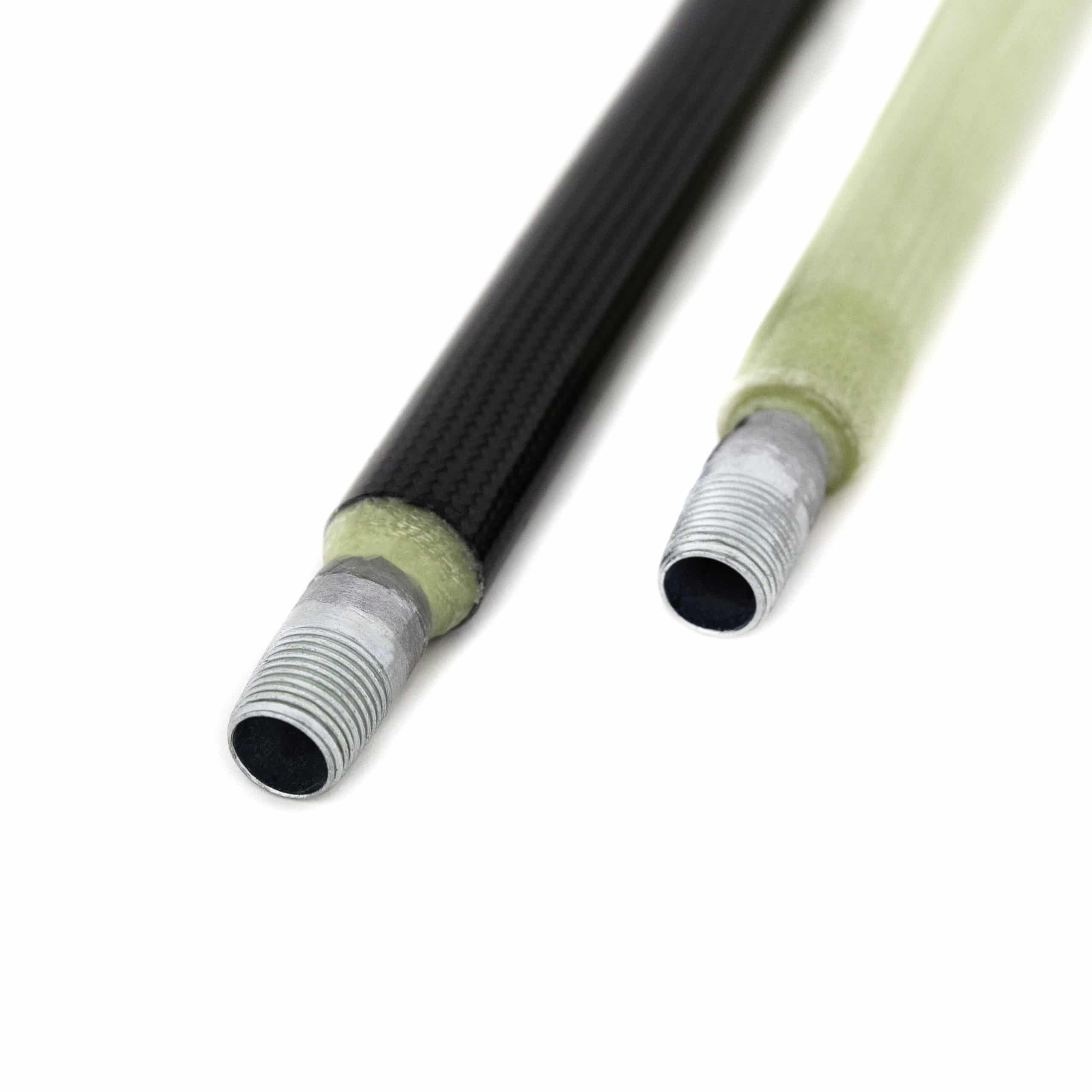
Post processing ability
The best composite tube in the universe is useless unless you can do something with it. At TUBETEC, we can mold in another part, be it a bracket, connecter, pressure fitting, etc. A part can be joined to the molded tube either during the TUBETEC molding process or as part of a secondary post-molding bonding process.